Qué es el granallado y dónde se aplica
El granallado es un tratamiento superficial mecánico realizado mediante la proyección de abrasivo metálico. El proceso de granallado implica el uso de abrasivos metálicos para limpiar y uniformar la superficie tratada, modificando la capa superficial preexistente a través de la abrasión por impacto y fricción.
Originalmente desarrollado para la retirada de la arena de moldeo y de los núcleos de piezas de fundición en las fundiciones, el granallado ha encontrado aplicación en múltiples sectores.
Se utiliza para preparar superficies para recubrimientos protectores como pintura en polvo o pulverización, metalización y teflón, así como para eliminar óxidos, calamina, corrosión y residuos de soldadura. Otros usos incluyen el decapado, el desbarbado, la limpieza posterior al estampado o el tratamiento térmico, así como generar rugosidad superficial.
Originariamente sviluppata per la rimozione della sabbia di formatura e delle anime dei getti fusi nelle fonderie, la granigliatura ha trovato applicazione in vari settori.
Differenza tra Granigliatura e SabbiaturaDiferencia entre granallado y arenado
Una de las principales diferencias entre el granallado y el arenado reside en el tipo de abrasivo utilizado y en la energía empleada en el proceso. Mientras que el granallado utiliza abrasivos metálicos lanzados a alta velocidad y permite obtener una limpieza profunda y una preparación precisa de las superficies metálicas, el arenado utiliza arena u otros materiales abrasivos inertes. El arenado también se puede realizar al aire libre sin recuperación del abrasivo y se utiliza para limpiar superficies no extremadamente contaminadas. El granallado emplea una mayor energía cinética, generada mediante turbinas, que permite a los abrasivos metálicos eliminar capas superficiales más duras y resistentes, como calamina, óxido y residuos de soldadura. El arenado, a pesar de ser eficaz para muchas aplicaciones, tiene un impacto menos intenso sobre la superficie tratada, lo que lo hace más adecuada para trabajos de limpieza superficial y preparación ligera.
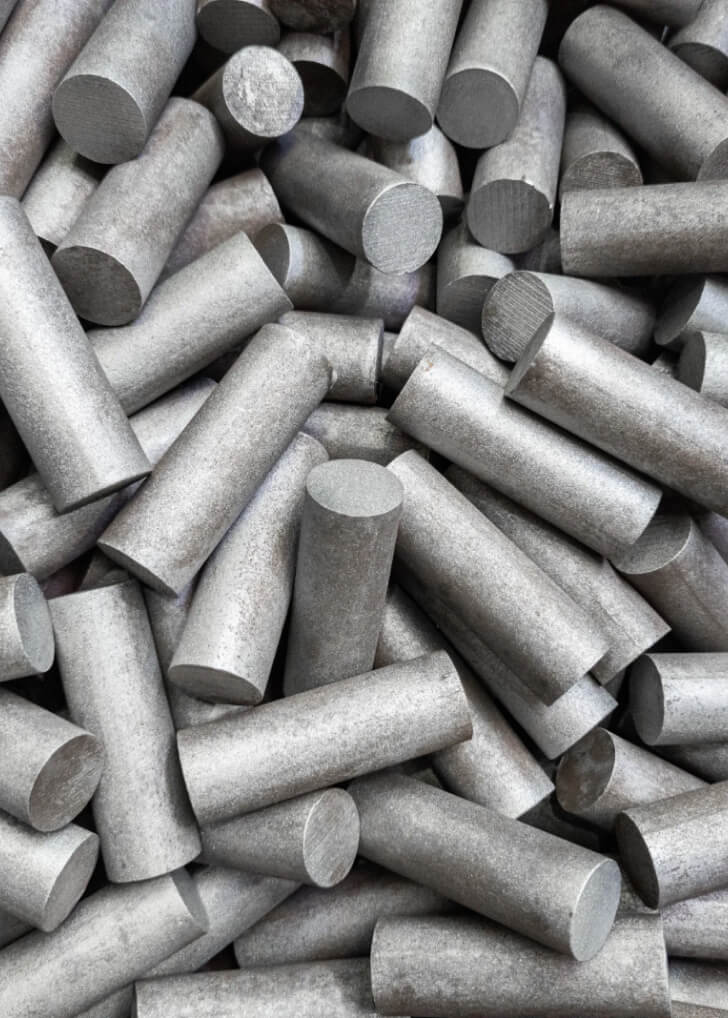
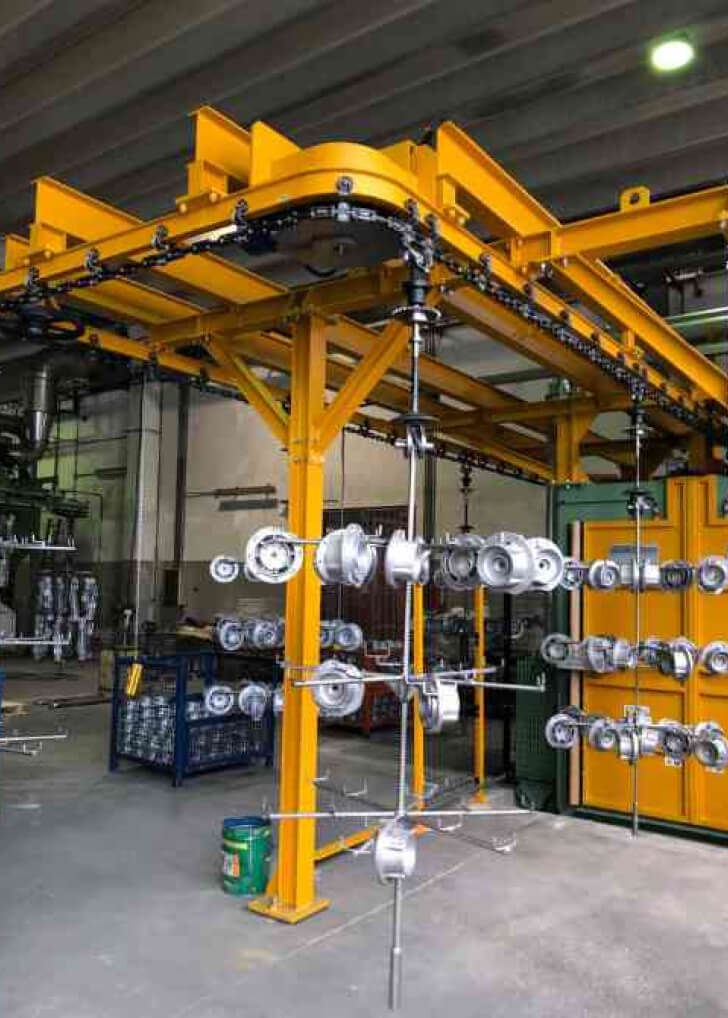
Las ventajas del proceso de granallado
El granallado ofrece numerosas ventajas, entre ellas el respeto de las normas de control de efluentes contaminantes. Se trata un proceso mecánico en seco que no implica el uso de productos químicos. El único agente contaminante que produce es el polvo producido por la cámara de granallado, que se filtra mediante la maquinaria adecuada conectada a la planta. Además, el granallado responde a la creciente demanda de productos estéticamente mejores y más funcionales.
- Contáctanos
Descubre más sobre nuestras soluciones de granallado
Para más información sobre el granallado y las instalaciones de granallado que podemos ofrecer, no dudes en ponerte en contacto con nosotros. Nuestro equipo de expertos está a tu disposición para ofrecerte asesoramiento personalizado y detalles técnicos.
Tipos de equipos de granallado y abrasivos utilizados.
Existen dos tipos de plantas de granallado y diferentes tipos de abrasivos utilizados en el proceso.
En las instalaciones de granallado con aire comprimido, el abrasivo se proyecta con precisión mediante aire comprimido, directamente sobre la superficie de la pieza a tratar, gracias a dispensadores específicos. Estos dispensadores se pueden controlar de forma manual o automática, garantizando una aplicación precisa y uniforme del tratamiento.
En las instalaciones de granallado de turbina, en cambio, la energía cinética necesaria para el proceso es generada por turbinas accionadas por motores eléctricos. Estas instalaciones se distinguen por su capacidad para tratar superficies de grandes dimensiones, gracias a la potencia de las turbinas que permite proyectar grandes cantidades de abrasivo a altas velocidades.
Son soluciones ideales para trabajos que se deben realizar incluso en piezas de considerable tamaño o complejidad.
En cuanto a los abrasivos utilizados, los metálicos se encuentran entre los más comunes. La granalla de acero, por ejemplo, se utiliza ampliamente en contextos industriales por su dureza y resistencia, lo que la hace perfecta para eliminar capas superficiales como la calamina. Para tratamientos más delicados o superficies que requieren un acabado más ligero, se prefieren abrasivos también metálicos pero de menor tamaño en acero inoxidable, cerámica y aluminio, empleando accesorios como los reguladores de velocidad de proyección (inversores).